В последние годы возросла значимость производства пластиковых водонепроницаемых коробок. Водонепроницаемые коробки защищают чувствительную электронику и оборудование от воды и других вредных факторов.
Эти специализированные коробки используются во многих отраслях промышленности. Они имеют значительные производственные процессы, охватывающие как наружное, так и промышленное применение.
Водонепроницаемые пластиковые коробки изготавливаются с использованием инновационных методов производства и проектирования. Процедура включает в себя ряд тщательно регламентированных процессов и проверок качества. Это гарантирует, что каждый ящик соответствует строгим критериям водонепроницаемости. Таким образом, пользователи могут извлечь пользу из понимания процессов производства этих важнейших изделий.
Что такое пластиковый водонепроницаемый ящик?
Пластиковые водонепроницаемые коробки защищают электрические устройства от воды, влаги и других вредных факторов. Большинство этих коробок изготавливаются из поликарбоната, АБС или ПВХ. Эти материалы были выбраны потому, что они служат долго и не боятся воды.
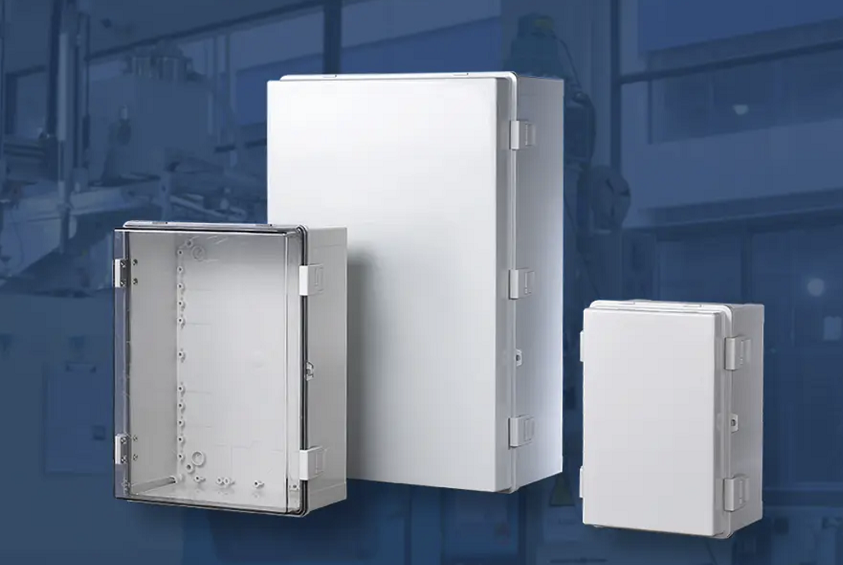
Независимо от погоды, водонепроницаемые коробки сохранят электрические детали в безопасности. Эти коробки гарантированно долговечны и изготовлены в соответствии со многими рейтингами NEMA и даже превосходят их . Это делает их отличными кандидатами для работы как внутри компании, так и за ее пределами.
Водонепроницаемые корпуса защищают гаджеты и другие вещи. В сложных условиях их можно использовать в качестве распределительных коробок или штепсельных розеток. Многие из них сделаны таким образом, что их можно использовать в качестве блоков питания как внутри, так и снаружи помещений. В обоих случаях есть что-то, что делает их выдающимися. В местах, где дождь или снег могут повредить электрооборудование, необходимы водонепроницаемые коробки.
Распространенные виды пластика, используемые при производстве электрических коробок
Электрические коробки часто изготавливаются из различных видов пластика. Ниже приведены распространённые виды пластика, используемые для изготовления электрических коробок:
1) АБС
ABS — это акрилонитрилбутадиенстирол. Это самый твёрдый синтетический полимер. Производители часто используют его для создания электрических коробок. Его предпочитают, потому что он прочный, не ломается и устойчив к воздействию тепла. Кроме того, его довольно просто формовать, красить или отделывать. Этот конструкционный пластик устойчив к ударам и сохраняет свой размер с течением времени. Благодаря этому он идеально подходит как для внутреннего, так и для наружного применения.
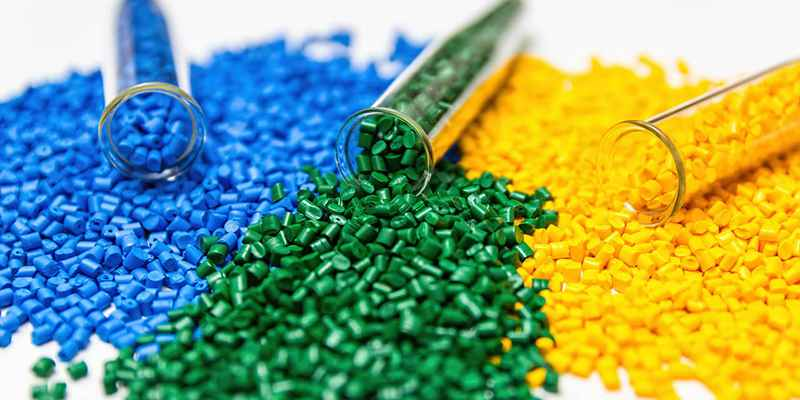
АБС-пластик гибкий, глянцевый и легко поддается обработке. Кроме того, его можно использовать при температурах до -4°F. ABS-пластик нельзя оставлять на солнце, поскольку он не устойчив к ультрафиолетовому излучению. Таким образом, он не идеален для защиты электроприборов на открытом воздухе.
2) Поликарбонат
Поликарбонат — лучший материал для изготовления электрощитов, поскольку он долговечен. Это популярный термопластик, отличающийся прочностью, стабильностью и прозрачностью. Он обеспечивает водонепроницаемость электрических устройств и устойчив к влаге.
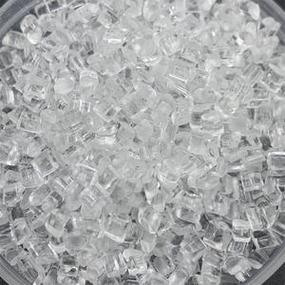
Кроме того, его можно легко раскрасить, что делает его хорошим выбором как с точки зрения функциональности, так и стиля. Технология часто использует его для создания внутренних и внешних корпусов, а также световодов. В отличие от АБС-пластика, поликарбонат не так легко разрушается под воздействием ультрафиолета. Кроме того, он не деформируется под воздействием солнечных лучей. Поликарбонат по своей природе огнестойкий. Он отлично защищает от электричества.
3) ПВХ
Поливинилхлорид отлично подходит для изготовления электрических коробок и недорогих изделий. Этот гибкий материал естественным образом предотвращает возникновение пожаров и изолирует электричество. ПВХ — жесткий пластик, идеально подходящий для корпусов, требующих хороших электроизоляционных свойств. Кроме того, его не повреждают химикаты, и он не подвержен возгоранию.
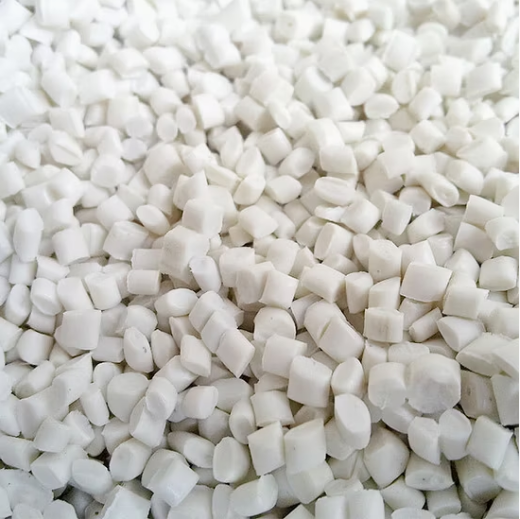
Устойчивость ПВХ к атмосферным воздействиям делает его идеальным для использования на открытом воздухе. Он выдерживает воздействие солнца, дождя и перепадов температур, не теряя своей формы. Материал обладает естественной устойчивостью к кислотам и многим химикатам. Поэтому в промышленных условиях он может прослужить дольше. ПВХ не такой ударопрочный, как поликарбонат или АБС. Однако для большинства повседневных задач этого вполне достаточно.
Использование правильных рейтингов IP
Степень защиты от проникновения называется просто IP-рейтингом. Стандарты определяют, насколько хорошо электротехнические шкафы защищают от ударов и воды. Ниже приведены некоторые стандартные рейтинги IP:
IP65 (защита от струй воды)
Корпуса со степенью защиты IP65 надежно защищают от струй воды низкого давления с любого направления. Для проверки этого явления устанавливают клетку, в которую со всех сторон льют струю воды. Эти коробки могут выдерживать воду, если ее лить прямо на корпус. Это делает их идеальными для использования на открытом воздухе в местах с умеренным воздействием воды.
Типичные сценарии включают места с периодическим распылением воды или места для уборки на открытом воздухе. Защита предотвращает попадание пыли, герметизируя все внутренние детали. Расстояние составляет 3 метра, диаметр сопла — 6,3 мм. Давление воды составляет 30 кПа, а расход — 12,5 л в минуту. Возможно, контейнеры IP65 не рассчитаны на полное погружение в воду. Но он отлично защищает вещи от случайных брызг воды.
IP66 (защита от мощных струй воды)
Корпуса со степенью защиты IP66 повышают уровень защиты. Обеспечивает защиту от мощных струй воды, обладает большей силой и объемом. Эти корпуса способны выдерживать сильные потоки воды, поступающие со всех сторон. Поэтому они подходят для эксплуатации в тяжелых промышленных условиях. Этот сорт пригоден для оборудования, используемого в морских условиях и на предприятиях химической переработки.
В течение трех минут струя воды диаметром 12,5 дюйма может создавать давление до 100 кПа и подавать 100 литров воды в минуту. Конструкция не допускает попадания воды в клетку даже при сильном давлении.
IP67 (защита от погружения на глубину до 1 м)
Этот стандарт требует полностью водонепроницаемой конструкции. Его можно временно погружать в воду на глубину одного метра на 30 минут. Этот стандарт обеспечивает полную защиту от пыли и хороший уровень водонепроницаемости.
Корпус со степенью защиты IP67 идеально подходит для использования на морских судах и в наружной электронике. Также подходит для оборудования, работающего во влажной или мокрой среде. Они идеально подходят для оборудования, которое может упасть в воду или работать в местах, подверженных затоплению. Благодаря этому классу внутренние детали остаются герметичными и безопасными даже при кратковременном воздействии воды.
IP68 (защита от длительного погружения)
IP68 обеспечивает наивысший уровень защиты от воды. Данный рейтинг допускает непрерывное погружение на глубину более одного метра. Точную глубину и продолжительность погружения производители определяют во время испытаний. Это может быть как несколько метров, так и длительное время.
Этот класс имеет важное значение для электроники, работающей в суровых водных условиях. Подходит для применения на больших глубинах и для оборудования, работающего под водой. Корпуса IP68 обеспечивают наилучшую защиту от воды, пыли и других проблем окружающей среды.
Шаги по изготовлению пластиковой водонепроницаемой коробки с использованием процесса литья под давлением
Литье под давлением превращает необработанный пластик в точно изготовленные водонепроницаемые коробки. Вот шаги по изготовлению пластиковой водонепроницаемой коробки методом литья под давлением:
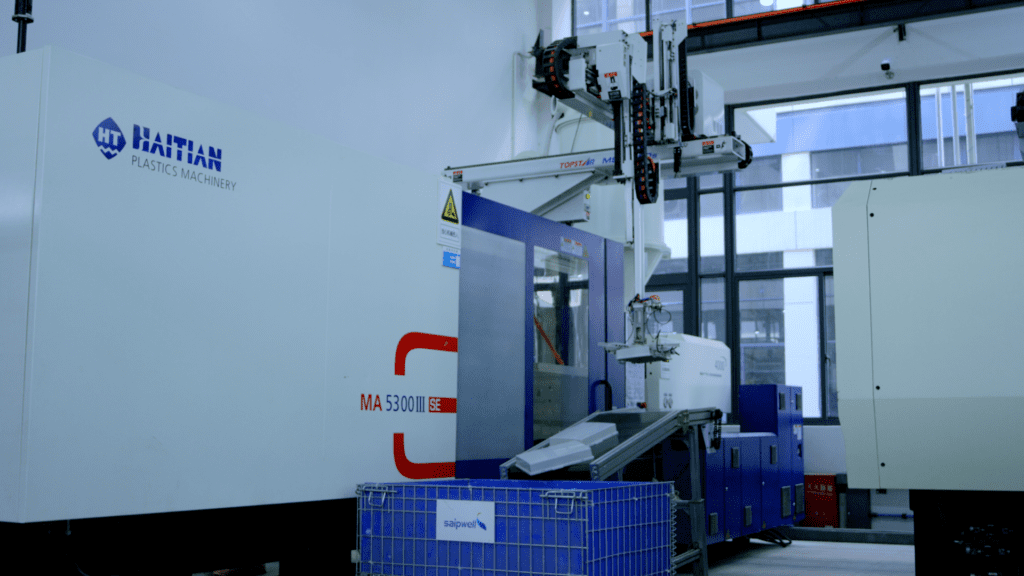
Шаг 1: Подготовка материала
Производители выбирают, какие пластиковые смолы использовать, исходя из желаемых свойств коробки. Собранный пластик имеет форму небольших гранул или пеллет. Полное высыхание исключает сырость, которая может повлиять на качество продукции.
После пропускания через воронку их расплавляют на сильном огне. После размягчения пластик прессуется в форму с одной или несколькими полостями для придания желаемой формы. Затем пластиковые детали оставляют остывать до тех пор, пока они не затвердеют, и форму для литья открывают. Новая пластиковая деталь выталкивается движущимися стержнями, пластинами или струей воздуха. Теперь он готов к использованию по своему первоначальному назначению.
Шаг 2: Подготовка формы
При изготовлении формы крайне важно уделять внимание каждой детали. Форма состоит из двух разных частей. Первая — это литьевая форма, которая формирует пластик, поступающий в машину. Во-вторых, эжекторная форма выталкивает готовое изделие из машины. Сделав это, он может продолжить свой путь по производственному циклу.
Технические специалисты проверяют форму на наличие дефектов и проверяют чистоту и гладкость стенок. Они также гарантируют отсутствие остатков материалов и отходов. Формы из закаленной стали или металла тщательно устанавливаются на литьевые машины. Для поддержания температуры во время формования проверяются охлаждающие каналы.
Шаг 3: Закрытие формы
Две половины формы точно совпадают, когда форма закрыта. Гидравлические или механические системы используют большое количество силы. Они помогают обеспечить полную герметичность и совмещение половин формы. Этот шаг очень важен для создания уплотнения, которое не позволит воде проникнуть внутрь или материалу вытечь во время сверления.
Чтобы сохранить форму формы, закрывающее устройство должно обеспечивать постоянное давление. Высокотехнологичные датчики следят за положением формы и давлением закрытия. Это гарантирует повторяемость и последовательность каждого производственного цикла.
Шаг 4: Впрыскивание материала
Для введения материала пластиковые гранулы необходимо нагреть до тех пор, пока они не расплавятся. Под высоким давлением (500–2000 бар) жидкий пластик подается в форму. Заполнение под высоким давлением гарантирует, что материал заполнит форму доверху. Он улавливает даже самые незначительные детали дизайна водонепроницаемого бокса.
Тщательный контроль скорости впрыска и давления позволяет удалить пузырьки воздуха и равномерно распределить материал. Кроме того, он сохраняет желаемые механические свойства конечного продукта.
Шаг 5: Упаковка
Тампонада — важный шаг, который следует за непосредственной инъекцией. Чтобы компенсировать усадку материала при охлаждении, в форму закачивают больше материала. Этот процесс гарантирует, что коробка останется именно того размера, который был разработан. Это позволяет устранить любые пробелы и другие проблемы, которые могли возникнуть.
Давление упаковки тщательно определяется с учетом типа пластика. Также уделяется внимание форме формы и размеру коробки. Интеллектуальные системы управления контролируют давление упаковки. Они регулируют его в режиме реального времени, обеспечивая плотность материала и структурную устойчивость.
Шаг 6: Охлаждение
Жидкий пластик должен остыть, чтобы он мог затвердеть и принять окончательную форму. Для обеспечения равномерного охлаждения в охлаждающих трубках формы циркулирует вода контролируемой температуры. Помимо воды, в нем могут циркулировать и другие охлаждающие вещества. Этот процесс занимает от 10 до 60 секунд в зависимости от толщины и материала коробки.
Правильное охлаждение коробки предотвращает ее деформацию. Тем самым обеспечивается стабильность размеров и сохранение точных водостойких свойств. Разница температур тщательно контролируется, чтобы минимизировать внутренние напряжения в материале.
Шаг 7: Извлечение детали
При этом затвердевшую водонепроницаемую коробку необходимо аккуратно, не повредив, извлечь из формы. Выталкивающие штифты или пластины осторожно выталкивают деталь из отверстия формы, не меняя ее форму. Система выпуска должна быть сделана так, чтобы равномерно распределять усилие. Это предотвращает накопление напряжения в одном месте, что может ослабить конструкцию коробки. Датчики в современных системах контролируют выброс, чтобы гарантировать последовательность и плавность.
Шаг 8: Проверка качества
Последний и самый важный этап производственного процесса — проверка качества. Для тщательной проверки каждого водонепроницаемого ящика используются передовые измерительные инструменты и методы. Для проверки точности размеров используются координатно-измерительные инструменты.
Затем проводятся испытания на водостойкость струей воды под давлением и погружением. Визуальный осмотр позволяет обнаружить дефекты поверхности, а специальные инструменты проверяют прочность уплотнения. К распространению допускаются только коробки, соответствующие самым строгим стандартам качества.
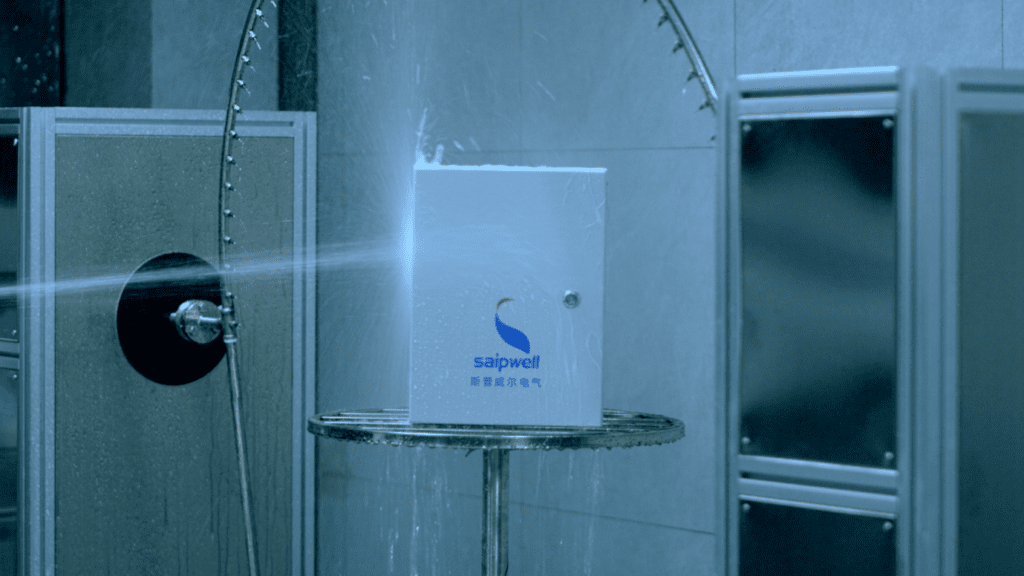
Передовые методы гидроизоляции, используемые в пластиковых коробках
Производители используют передовые методы для обеспечения водонепроницаемости пластиковых коробок. Ниже приведены передовые технологии обеспечения водонепроницаемости, используемые в пластиковых коробках:
1) Уплотнительные кольца
При производстве пластиковых коробок уплотнительные кольца являются простым, но очень эффективным способом защиты от попадания воды. При нажатии между двумя поверхностями эти круглые уплотнители обеспечивают идеальную герметизацию. Обычно они изготавливаются из силикона, резины или искусственных эластомеров. Поскольку их поперечное сечение имеет сферическую форму, они могут работать с слегка несовершенными поверхностями. Таким образом, обеспечивается превосходная герметизация.
Пока материал гибкий, он может сохранять герметичность в различных условиях. Сборка уплотнительных колец без перекручивания или перепутывания может оказаться сложной задачей. Даже небольшая ошибка может сделать гидроизоляцию менее эффективной.
2) Изготовленные на заказ резиновые прокладки
Изготовленные на заказ резиновые уплотнители — более гибкий способ сохранить пластиковые коробки сухими. В отличие от обычных уплотнительных колец эти прокладки изготавливаются с учетом точной формы закрывающей поверхности коробки. Это облегчает соединение и снижает вероятность потери уплотнений. Для обеспечения точности посадки и водонепроницаемости на протяжении всего процесса проектирования используется компьютерное моделирование. Форма уплотнения тщательно продумана для равномерного распределения давления.
Помимо преимуществ, этот метод имеет некоторые проблемы. Поскольку уплотнитель должен быть плотным, изделие может казаться больше, что не всегда хорошо. Это хороший выбор для небольших объемов производства, но его сборка может занять некоторое время.
3) Формование
Многослойное формование позволяет интегрировать уплотнительные элементы непосредственно в процесс производства коробки. При этом методе мягкий, гибкий материал формуется на твердой пластиковой основе. Создает водостойкое, гладкое и очень эффективное уплотнение.
Уплотнение встраивается в изделие в процессе производства, поэтому сборщикам это делать не нужно. Это не только ускоряет процесс, но и сокращает количество ошибок, которые допускают люди. Формование обеспечивает точный контроль формы уплотнения. Таким образом, обеспечивается стабильная производительность в различных условиях окружающей среды.
Заключительные мысли!
Пластиковые водонепроницаемые коробки имеют решающее значение для защиты чувствительного электрооборудования во многих отраслях. Производители используют самые современные материалы и процессы для создания прочных и соответствующих требованиям коробок.
Эти методы крайне важны для понимания производителями и пользователями. Это показывает, насколько важны надежность и качество для обеспечения безопасности дорогих гаджетов. Все больше людей хотят иметь эти критически важные средства безопасности. Таким образом, новые усовершенствования позволят этим защитным опциям работать лучше и служить дольше.
Saipwell производит высококачественные пластиковые водонепроницаемые ящики. Мы предлагаем варианты индивидуального изготовления и изготавливаем пластиковые коробки различных форм и размеров. Свяжитесь с нами , чтобы получить мгновенное предложение!